Remote Condition Monitoring of Critical Equipment
Omron’s Predictive Maintenance Solutions
Predictive maintenance is the key to reducing unplanned downtime and operational costs
To address significant changes in business conditions, urgent workplace transformation is imperative. Relying less on skilled maintenance personnel and embracing advanced technology is key.
Nevertheless, overcoming cost and technological hurdles can pose challenges. Omron’s solution addresses these challenges by continuously monitoring and analyzing real data through frequent checks.
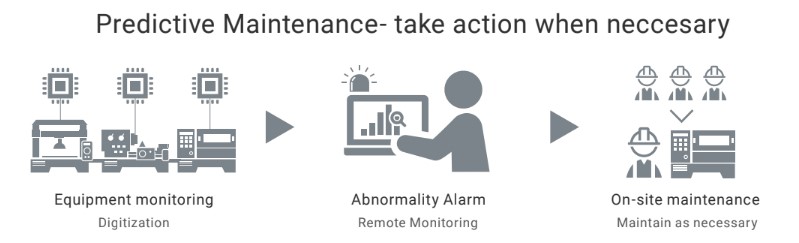
Remote monitoring of critical equipment using condition monitoring devices
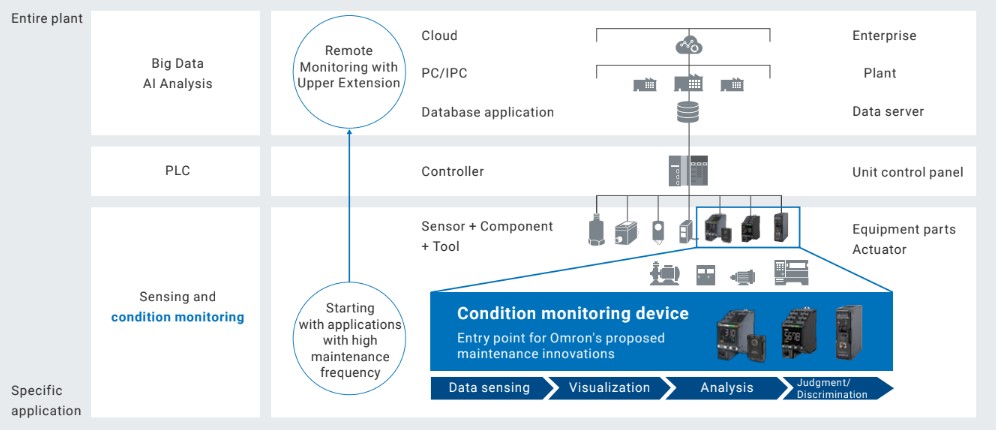
Resolve issues through condition monitoring
Our predictive maintenance solution replicates skilled maintenance engineers’ analysis by retrofitting existing equipment and enabling remote monitoring. This technology simplifies equipment analysis, converting measurement data into alarms, facilitating faster issue responses.

How condition monitoring works

Easily installs on existing equipment
Omron’s predictive maintenance solutions are simple to integrate into existing equipment with minimal to no need for modifications.
Remote monitoring made simple
Each predictive maintenance solution includes user-friendly monitoring software, enabling easy operation. The controller performs analysis, eliminating the need for manual assessment.
Predictive Maintenance Applications
- Detecting worn components on homogenizer
- Detecting cooling water circulation pump deterioration
- Detecting hydraulic valve wear on a stamping press
- Detecting control panel abnormalities using IoT
K6CM motor condition monitoring device
Effect: Eliminates maintenance and inspection services essential for stable production of beverages
Beverage manufacturers encounter significant losses due to equipment failures, mainly stemming from worn homogenizer components causing both downtime and contamination. A scarcity of skilled maintenance engineers posed challenges in detecting failures early. As a result, the company resorted to frequent part replacements as a preventive measure, proving to be both inefficient and costly. The introduction of the K6CM motor condition monitor empowered maintenance engineers to monitor component degradation, enabling prompt issue resolution. This strategy curbed unnecessary component replacements and eliminated frequent inspections, ultimately enhancing cost-effectiveness and operational efficiency for the manufacturer.

FROM: Manually checking motor current readings
Motor current was manually measured with a current meter, but inconsistencies and abnormal conditions went unnoticed. Parts were replaced every 3 to 6 months, with an annual overhaul.
TO: Remote motor current distortion analysis
The equipment autonomously assesses component deterioration, continuously monitoring conditions from a distance, eliminating the need for routine inspections and allowing for planned part replacements.

Analyzing changes beyond the current value within the current waveform can reliably identify abnormalities by converting them into degrees of deterioration.
Customer Feedback:

K6CM motor condition monitoring device
Effect: Reduction in on-site maintenance inspections for cooling water circulation pumps.
A cooling water circulation pump at a water treatment plant operates continuously, posing production risks in case of failure. Prior to K6CM installation, manual inspections by experienced engineers using vibration testers were necessary. However, with the K6CM, predictive maintenance became possible, eliminating the need for equipment shutdowns. Consequently, the customer obtained more precise and consistent pump data.
FROM: Periodic on-site inspection by a maintenance engineer using a vibration tester
Periodic inspections occurred due to uncertain breakage timing. However, failures sometimes occurred between these inspections.
TO: Remote monitoring of abnormal vibration conditions and receiving alerts of degradation
The K6CM enables remote detection of deterioration tendencies and central monitoring, significantly reducing maintenance man-hours by addressing issues promptly.
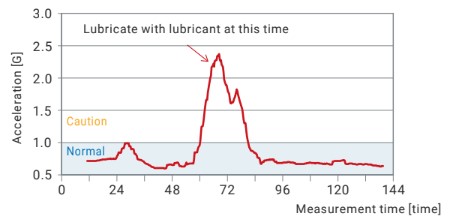
Precisely measuring high-frequency vibrations, then converting them into speeds and accelerations, enables early detection of anomalies.
Customer Feedback
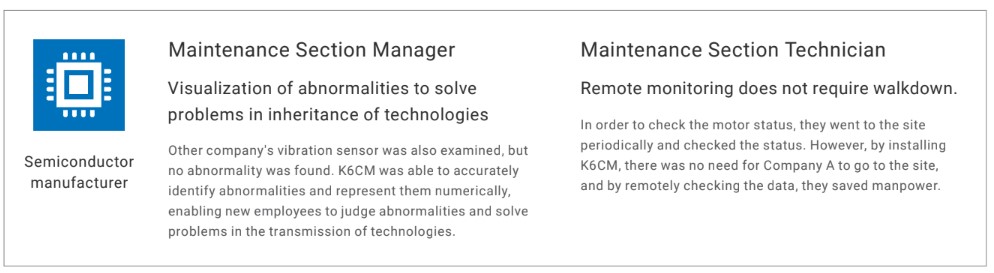
K6PM-TH thermal condition monitoring device
Effect: Faster response to hot spots developing in hydraulic system
A global automotive manufacturer experienced unplanned downtime from hydraulic valve failure due to contamination, raising valve surface temperatures. Despite manual temperature checks by the maintenance engineer, continuous monitoring was absent.
To tackle this issue, they implemented the K6PM thermal condition monitor, ensuring ongoing monitoring of hydraulic valve surface temperatures. This enables the maintenance engineer to promptly receive temperature increase alerts, eliminating the need for routine temperature checks.
FROM: Manual thermal inspection of hydraulic temperatures on stamping press
Limited manual thermal inspections hindered trend identification and hot spot detection, ultimately resulting in the hydraulic valve’s premature failure.
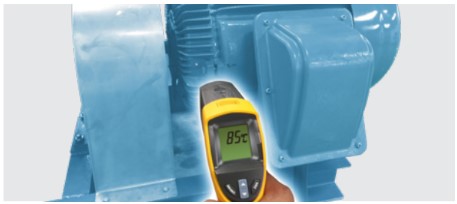
TO: Continuous monitoring of hydraulic valve temperature using K6PM’s thermal image sensors
Maintenance engineers can enhance reliability by remotely monitoring equipment temperature changes over time rather than relying solely on manual thermal inspections. This approach enables faster issue response.

The system detects both ambient and measurement temperatures concurrently, monitoring the pure temperature change of the object using a differential temperature detection algorithm.
Customer Feedback

S8VK-X IoT power supply
Effects: Remote monitoring of automotive production line equipment for improved predictive maintenance
In automotive assembly facilities with multiple control panels, maintenance engineers face challenges in manually detecting issues, especially component deterioration. To minimize unplanned downtime, engineers often preemptively replace components.
However, integrating the S8VK-X power supply provides visibility into its health and downstream circuit details, improving predictive maintenance and eliminating unnecessary component replacements.

FROM: Manual inspection of control panel and unnecessary replacement of components
The power supply in a production facility is vital as it provides electricity to control components. It must be replaced within its lifespan. Nevertheless, evaluating deterioration and identifying the ideal replacement time is challenging.

TO: Remote monitoring of equipment health and maximizing power supply life
The installed electrolytic capacitor’s temperature was measured, and S8VK-X predicted the replacement time. Communication enables data retrieval, facilitating centralized monitoring from the office for each S8VK-X’s status.
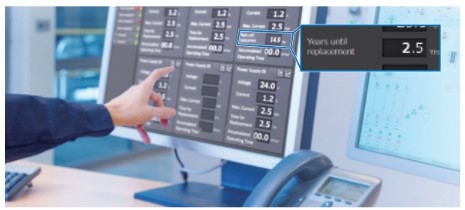
Assess life part deterioration based on internal temperature and communicate the replacement schedule accordingly.
Customer Feedback

Omron’s Unique technology that eliminates the need for frequent inspections from maintenance personnel
Technology for motor condition monitoring
Motor abnormalities, including wear, insulation issues, misalignment, and imbalance, need assessment. Experienced engineers traditionally use vibration and temperature testing equipment.
Omron’s K6CM, using sensing technology, can detect these issues, analyze failure modes, and remotely notify maintenance via Ethernet IP or Modbus TCP.

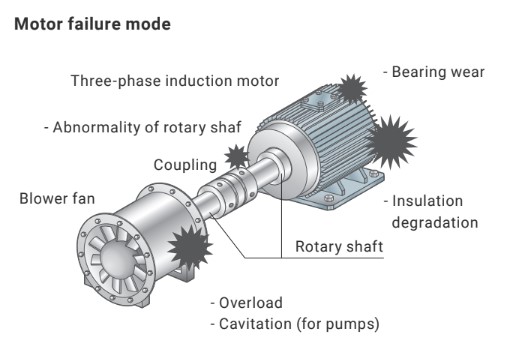

Degradation detection algorithm
The “degree of deterioration” assesses deviations from the ideal motor current state, analyzing current waveform data affected by motor and equipment issues. It detects problems such as pump cavitation, foreign object intrusion, misalignment, and imbalance.
By quantifying specific frequency components impacting the motor’s axis, it efficiently identifies consistent errors, remaining sensitive even in environments with inverter noise. This value streamlines motor abnormality detection, supporting experienced personnel.
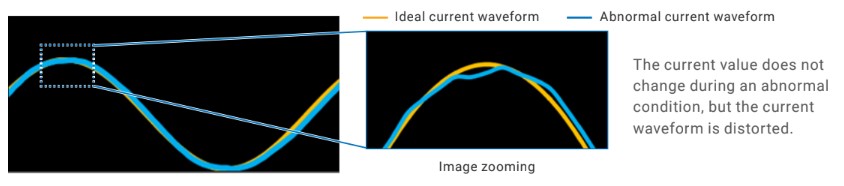
Detect hot spots remotely using thermal infrared sensors
Hot spots in control panels result from various factors, including overheating, insulation breakdown, and loose connections, potentially leading to electrical fires and equipment damage.
The K6PM-TH thermal condition monitoring device offers continuous hot spot monitoring and alerts maintenance engineers about temperature increases.

Arrival temperature prediction algorithm
On-site issues
Errors during periodic inspections can delay detection, potentially leading to ignition, smoke generation, or equipment stoppage. Additionally, even with continuous data collection, there might not be sufficient time to respond when thresholds are exceeded.
Solution
The temperature to be reached is predicted from the tendency of the temperature to rise, and the abnormal temperature is judged early.

Differential temperature detection algorithm
On-site issues
Unable to calculate the accurate temperature variation of a device measured under an environment to be affected by an outside air temperature. If the ambient temperature changes, the temperature of the equipment to be measured also changes significantly.

Solution:
Measuring ambient temperature from the sensor’s interior and continually calculating the differential temperature from the device temperature helps detect and identify abnormalities like temperature increases effectively.

Maintenance tips
Relay Timers
Issue: When the equipment abruptly halted, it resulted in the malfunction of both the relay and the timer installed within it.
Cause: The appropriate relay timer for the load may not be selected
Commonly, “bigger” technology like personal computers and smartphones exists, but relays within timers and monitoring devices necessitate tailored selection based on load.
This arises from varying demands on relay structure due to high or low current. Essentially, relays exhibit “scalability.” Prudent selection enhances relay longevity, minimizes contact issues, and bolsters circuit reliability.
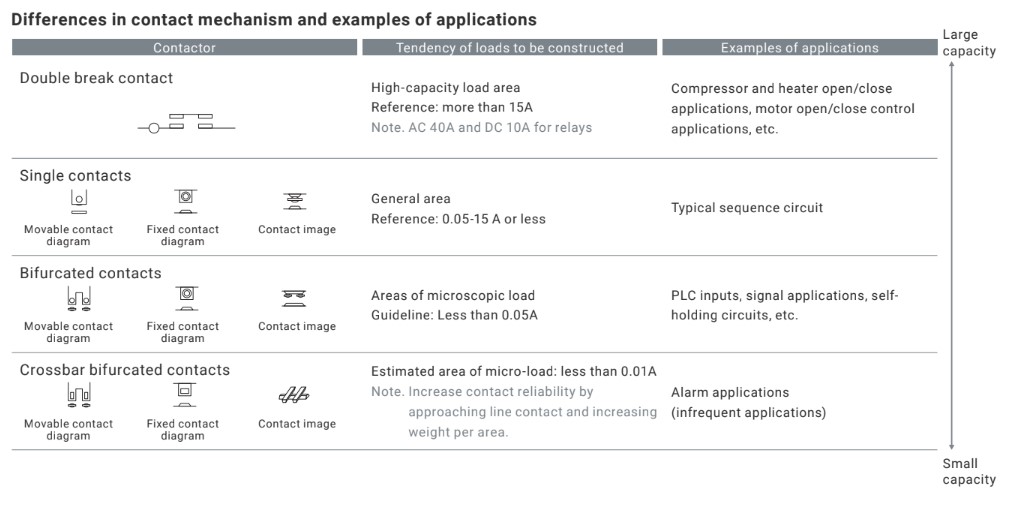
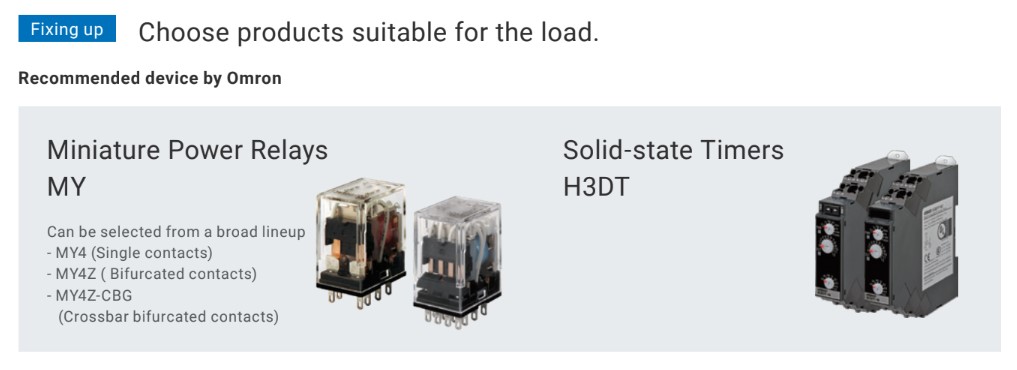
Measuring and Monitoring relays
Issue: If the monitoring relay is used in an environment where noise is severe, such as an inverter, it is likely to break quickly.

Cause: Be due to the power supply circuit
Many of the monitoring relays use condenser droppers, and heat generation increases due to high frequency noise. If the fever increases, the following risks may occur.
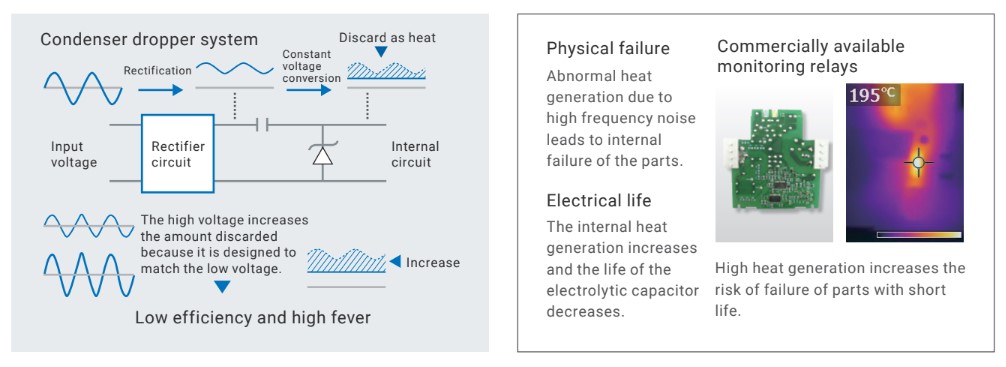
Fixing up: Select products with switching method
