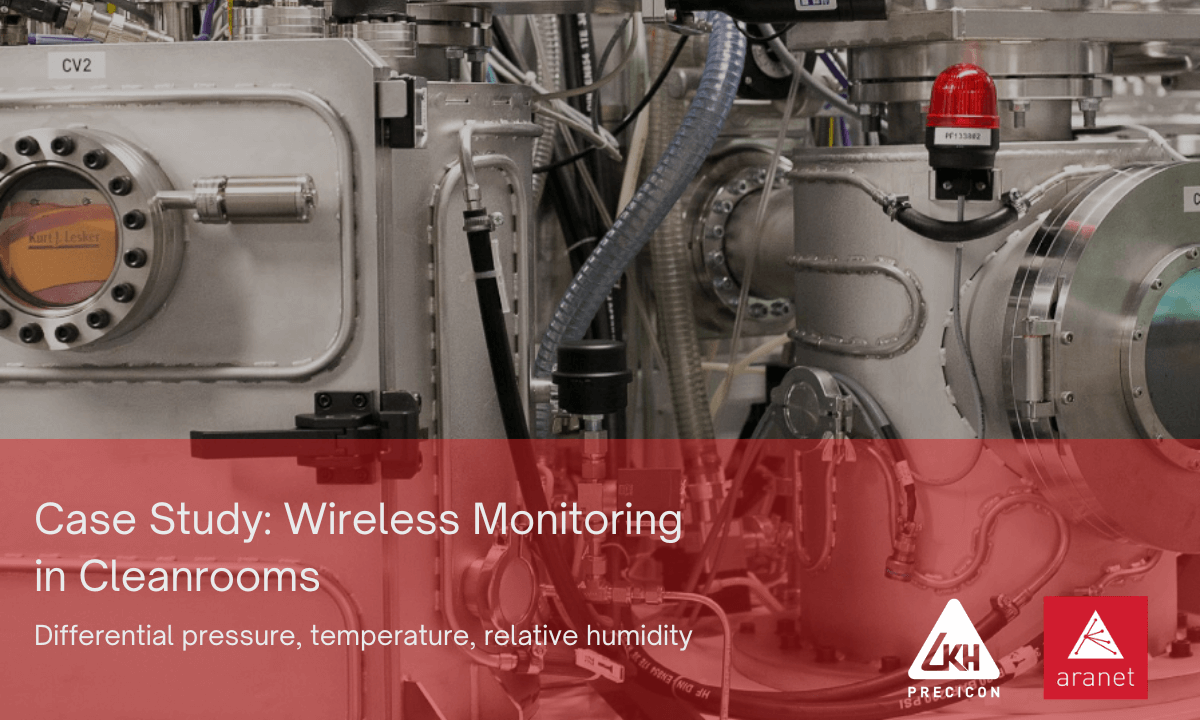
The Institute of Solid-State Physics, University of Latvia (ISSP UL), renowned for materials sciences, established a cleanroom in 2012. It contains various tools for cleaning, surface preparation, electron beam, photolithography, thin film deposition, and wet/dry etching. Moreover, they have incorporated the Aranet IoT solution to monitor the cleanroom environment. This ensures stable temperature, appropriate microclimate, and sustained pressure differences for both personnel and equipment.
A cleanroom is a controlled environment that minimizes particle presence. It regulates parameters like temperature, humidity, pressure, with importance placed on temperature, humidity, and differential pressure in ISSP UL cleanrooms.

The entire system used by the institute contains:
- Aranet PRO 100 base station
- Several Aranet T/RH sensors
- Several Aranet T-probe sensors
- Few Aranet CO2 sensors
- Several Aranet differential Pressure sensors
Maintaining positive pressure in cleanrooms prevents pollution. ISSP UL faced a challenge, relying on manual checks for pressure differences. The Aranet Differential Pressure sensor enables remote monitoring and faster response to issues. If pressure decreases, they can quickly identify ventilation or other problems.
“Last Monday we had an issue where the ventilation controller shut down at 5AM. The temperature started to climb only after 2 hours, but we saw the differential pressure problem immediately so we could react,” says Valdis Korsaks, a Cleanroom Manager at the institute, who is also in charge of this project.
The laboratory team discovered an additional application for the differential pressure sensor: monitoring fume hoods and other air extraction systems. A fume hood, used for limiting exposure to hazardous substances, must have functional ventilation. Aranet sends an alarm if ventilation stops, ensuring safety for lab workers.
Measuring CO² primarily ensures the well-being of cleanroom occupants. The institute acquired CO² sensors to safeguard researchers’ health. Prolonged exposure to high CO² levels can harm cognitive abilities and overall health, especially in enclosed environments like cleanrooms, prone to CO² buildup. Fortunately, they discovered that air exchange functions well, maintaining CO² levels within acceptable limits.
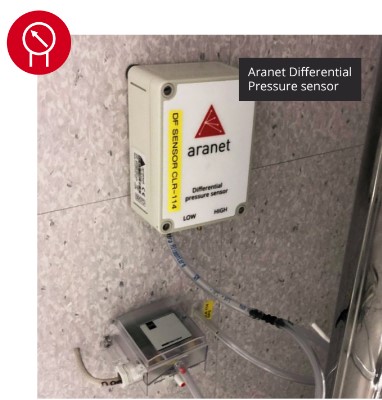
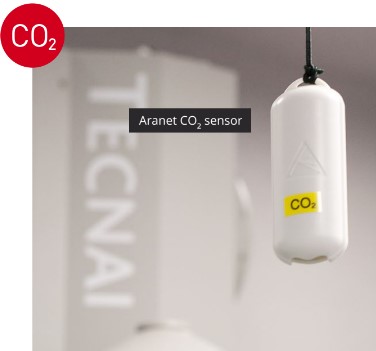
Monitoring temperature is crucial for equipment functionality. Electron microscopy and lithography are temperature-sensitive; disruptions lead to significant costs and research time loss. Aranet sensors enable timely response and issue resolution. Additionally, relative humidity is critical for lithography; the Aranet T/RH sensor measures both parameters, ensuring process success.
“Before Aranet we had control but didn’t have monitoring – meaning that we could set the parameters and set points for ventilation. We didn’t know what was happening, the lithography got destabilized and we didn’t know why, so we started to look for solutions,” remembers Valdis.
“Now the situation is greatly improved – before installing Aranet we could assure that our cleanroom had a ±2-degree temperature stability. With the help of Aranet sensors we can ensure that the temperature does not vary by more than ±0.2 degrees.
I would definitely recommend Aranet to other cleanrooms and laboratories because it is a simple, easy to use wireless system with a great price/performance ratio. You can place the sensor anywhere – near any device that you wish to measure, and the alarm functionality helps you avoid very costly problems.”