Temperature Controllers
What is a Temperature Controller?
A Temperature Controller maintains equipment temperature by comparing sensor data with a set point, making calculations based on deviations. Controllers handling different sensor signals, such as humidity, pressure, and flow rate, are called Controllers, and those with electronic capabilities are termed Digital Controllers.
These Controllers receive sensor signals, regulating heaters and devices for temperature control. They extend to humidity, pressure, and flowrate control, with Omron offering temperature and humidity sensors.
Temperature Control
Temperature Controllers aim to align the process value with the set point, but the response varies depending on the controlled object and method. Ideally, a response like Figure (2) is preferred, achieving the set point quickly without overshooting. However, in some instances, as shown in Figure (1), a rapid temperature increase with overshoot is necessary, while Figure (3) illustrates situations where a slow temperature rise is required.
(1) The process value settles around the set point while continuously oscillating above and below it.
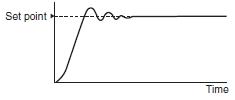
(2) Proper response
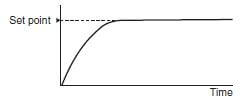
(3) Response where the process value slowly reaches the set point
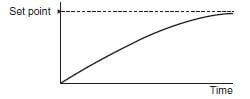
Temperature Control Configuration Example
The following example describes the basic configuration for temperature control.
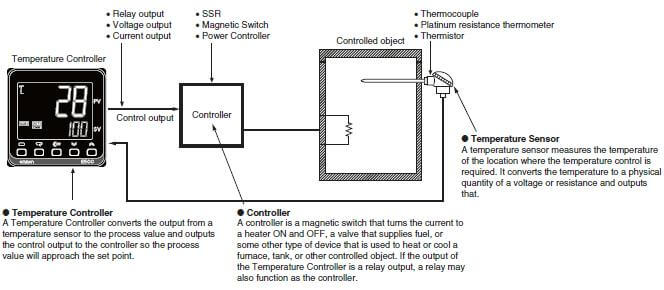
Temperature Controller Principle
The figure illustrates a feedback control system for temperature regulation. Key components are integrated into the Temperature Controller, allowing the assembly of a feedback control system for temperature control by combining it with a suitable controller and temperature sensor for the controlled object.
Configuration of a Feedback Control System
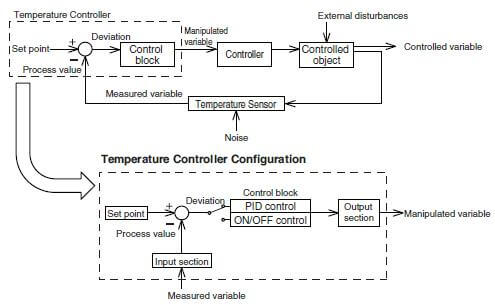
Characteristics of the Controlled Object
To ensure effective temperature control, it’s essential to comprehend the thermal characteristics of the controlled object before choosing a Temperature Controller or temperature sensor.
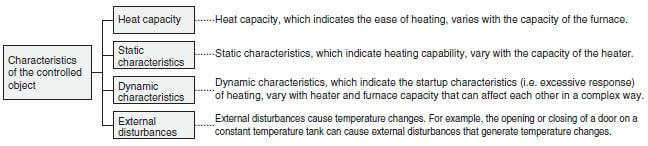
Control Methods
[ON/OFF Control Action]
The graph illustrates ON/OFF control action, where the output switches ON to provide heater power when the process value is below the set point and OFF when it’s above. This method maintains constant temperature using two values (0% and 100% of the set point), known as two-position control action.
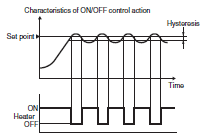
[P Action (Proportional Control Action)]
Proportional control action, or P action, reduces the deviation between the process value and set point by generating a control output proportional to the deviation within a set proportional band. Here’s how it works:
- Within the proportional band, a manipulated variable proportional to the deviation is produced.
- If the process value falls below the proportional band, a 100% manipulated variable is generated.
- If the process value exceeds the proportional band, a 0% manipulated variable is generated.
Unlike ON/OFF control, proportional control offers smoother operation by gradually adjusting the output near the set point based on deviation. However, using proportional action alone may result in temperature stabilizing away from the set point (offset).
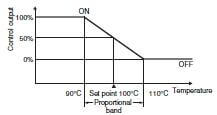
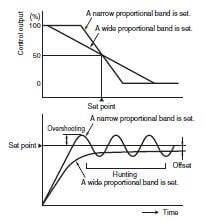
[I Action (Integral Control Action)]
I action (integral action) adjusts the manipulated variable based on deviation size and duration. Proportional action alone results in temperature stabilization but with an offset. Combining proportional and integral actions reduces deviation over time, aligning the process value with the set point.
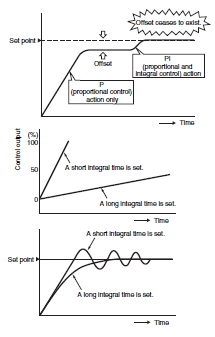
[D Action (Derivative Control Action)]
D action, or derivative action, responds to abrupt process value changes, like external disturbances, to swiftly restore control to its initial state.
While proportional and integral actions delay corrections for abrupt changes, derivative action compensates, offering a significant variable for rapid disturbance responses.
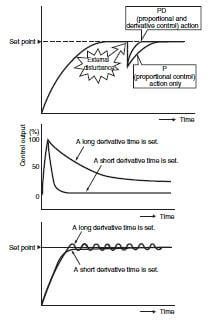
[PID Control]
PID control combines proportional, integral, and derivative actions. It ensures smooth temperature control, prevents hunting with proportional control, adjusts for automatic offset with integral control, and enables rapid response to external disturbances through derivative control.
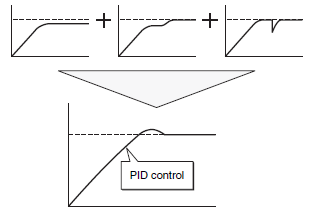
[Two PID Control]
Conventional PID control uses a single block, causing oscillations with certain parameter values. Two PID control balances set point and disturbance responses for optimal performance.
(1) PID Control
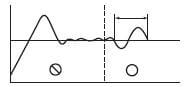
Response to the set point will be slow if response to the external disturbance is improved.
(2) PID Control
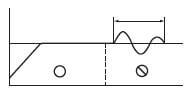
Response to the external disturbance will be slow if response to the set point is improved.
(3) 2 PID Control
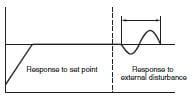
Controls both the set point and the external disturbance response.
What is a Temperature Sensor?
A Temperature Sensor measures the necessary temperature, converting it into a voltage or resistance for output.
Temperature Measurement Categories
There are two categories of temperature measurement, as described below.
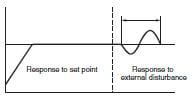
Thermocouple
Principle
A thermocouple is a temperature sensor exploiting the Seebeck effect, producing thermoelectromotive force based on temperature variation between metal ends joined together. A combination of metals with a consistent thermoelectromotive force is termed a thermocouple.
The Law of Intermediate Temperatures and the Law of Intermediate Metals
A thermocouple generates potential difference due to dissimilar wire materials and temperature difference between junctions.
The Law of Intermediate Temperatures and Metals confirm temperature variations and different metals between junctions don’t affect the potential difference when conditions are consistent.
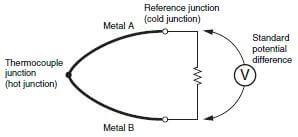
Thermocouple Types
Thermocouples vary based on the metals they employ, with types K, E, J, and T using base metals, and types B, R, and S using noble metals. Selection depends on temperature, environment, and accuracy requirements, with types K, J, and R being frequently preferred.
Characteristics of Thermocouple Potential Difference
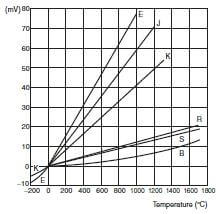
Compensating Lead Wire
Extending thermocouple temperature sensor leads with copper wire leads to notable temperature inaccuracies. Compensating conductors, which replicate the thermoelectromotive force of the thermocouple, are necessary for extensions.
These cables are available in general-purpose (-20 to 90°C) and heat-resistant (0 to 150°C) variants, conforming to JIS standards for operating temperatures. Selecting the correct compensating conductor that matches the thermocouple type is crucial.
Platinum Resistance Thermometer
Resistance Thermometer
This device utilizes the connection between metal resistance and temperature, necessitating specific material attributes: a high temperature coefficient of electrical resistance, linearity, stability, and suitability across a wide temperature range. Platinum best fulfills these criteria and is recommended by JIS.
Platinum Resistance Thermometer
This device relies on platinum’s temperature-dependent resistance increase. In the past, JPt and Pt represented different platinum resistance thermometers under JIS standards. Although JPt is no longer common, some systems still use it, leading temperature controllers to offer support for JPt. However, Pt and JPt have unique characteristics, requiring accurate input type settings for temperature controllers.
Compensating Lead Wire Types
The Pt 100 platinum resistance thermometer has 100 Ω resistance at 0°C. Its low standard resistance ratio (R100/R0 = 1.3851) is susceptible to lead wire resistance. To counter this, a common approach is using a three-wire resistance thermometer wiring to eliminate compensating wire resistance effects.
Three-wire Resistance Thermometer
To negate the impact of resistance when extending lead wires, one resistance conductor links to two wires, while the other connects to a separate wire. OMRON adopts this configuration for all their three-wire platinum resistance thermometers.
Connection of Three-wire Platinum Resistance Thermometers
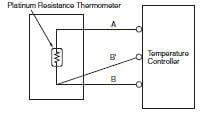
Interested to find out more about Omron Temperature Controllers? Feel free to contact us!