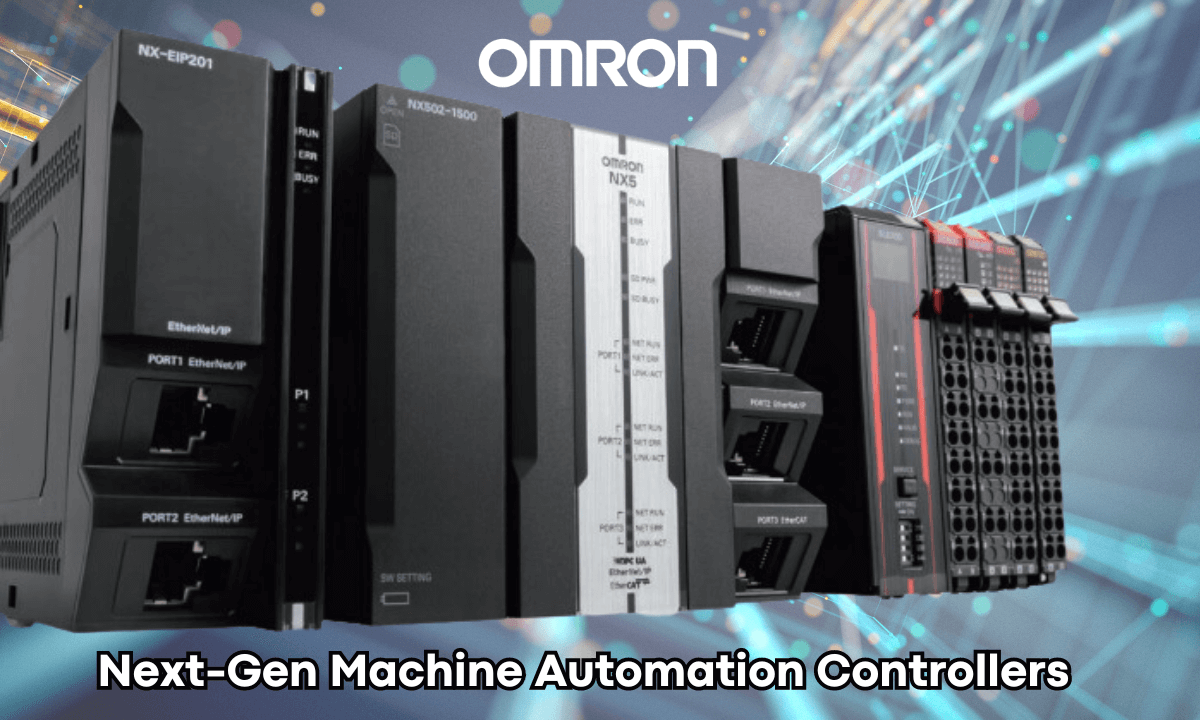
What is a Machine Automation Controller?
The NJ/NX-series Controllers are the next-gen machine automation controllers, offering essential functionality and high-speed performance for precise control. Additionally, they meet rigorous industrial safety, reliability, and maintainability standards.
These controllers seamlessly integrate features from previous OMRON PLCs. Moreover, they add vital motion control capabilities, enabling synchronized control of diverse I/O devices via high-speed EtherCAT®. This includes safety devices, vision systems, and motion equipment. Consequently, users benefit from enhanced flexibility and efficiency in their automation processes.
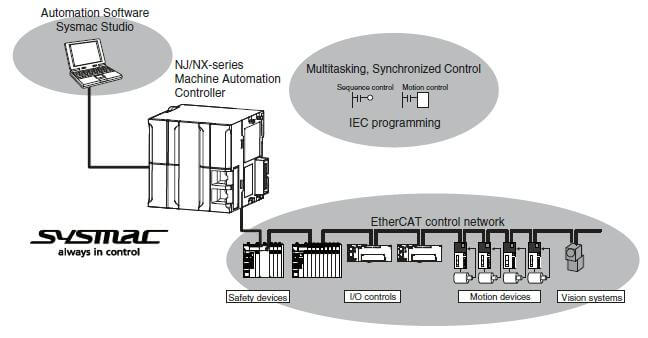
Features
Hardware Features
Standard-feature EtherCAT Control Network Support
All CPU Units feature an EtherCAT master port, facilitating efficient communication through this high-speed industrial network system, based on Ethernet. Additionally, EtherCAT achieves short fixed communication cycles, allowing the connection of various machine control devices such as I/O systems, servo drives, inverters, and vision systems to a standard EtherCAT control network.
Support for EtherCAT Slave Terminals
EtherCAT Slave Terminals not only help save space but also allow you to construct versatile systems using the diverse range of NX Units available. Furthermore, these terminals facilitate seamless integration, making it easier to optimize your system’s performance.
Achieving a Safety Subsystem on EtherCAT
Integrate safety controls into an EtherCAT-based sequence and motion control system using NX-series Safety Control Units.
CJ-series Units
NJ-series CPU Units facilitate the integration of CJ-series Basic I/O Units, Special Units, and EtherCAT network slaves onto the I/O bus. Additionally, they empower seamless communication and coordination between these components, ensuring efficient and streamlined operations.
Standard-feature EtherNet/IP Communications Port
All CPU Units feature an EtherNet/IP port, thereby enabling EtherNet/IP communications. This network, which utilizes Ethernet, serves as a multi-vendor industrial option. It is particularly suitable for Controller-to-Controller or field networks. Moreover, standard Ethernet technology facilitates seamless connectivity with various general-purpose Ethernet devices.
Standard-feature USB Port
You can establish a direct USB connection between a computer running the Support Software and the CPU Unit.
Standard-feature SD Memory Card Slot
In the user program, you can access an SD Memory Card mounted in the CPU Unit.
Highly Reliable Hardware
The NJ/NX-series Controllers not only offer the hardware reliability and RAS functions typically expected from a PLC, but they also provide advanced features for seamless integration. Moreover, their robust design ensures optimal performance in diverse industrial applications.
Parallel Execution of Tasks with a Multi-core Processor
The NX701-[][][][] CPU Unit boasts a multi-core processor, allowing parallel task execution for high-speed control of large-scale devices.
Software Features
Integrated Sequence Control and Motion Control
The NJ/NX-series CPU Unit seamlessly integrates sequence and motion control, facilitating simultaneous execution. Furthermore, these essential functions, including I/O refreshing, seamlessly unfold within the same control period. This synchronization is meticulously aligned with EtherCAT data communication, guaranteeing not only precise sequence and motion control but also minimizing any potential deviation.
Multitasking
Programming Languages Based on the IEC 61131-3 International Standard
The NJ/NX-series Controllers support language specifications rooted in IEC 61131-3, enhanced with OMRON’s modifications.
They include motion control instructions aligned with PLCopen® standards and an instruction set (POUs) compliant with IEC rules.
Programming with Variables to Eliminate Worrying about the Memory Map
In the same manner as advanced computer programming languages, data is accessed through variables. Moreover, the CPU Unit automatically allocates memory to your created variables, thereby eliminating the need to recall physical addresses.
A Wealth of Security Features
The NJ/NX-series Controllers boast a multitude of security features. These include operation authority settings and the restriction of program execution with IDs. Moreover, these controllers provide robust protection mechanisms to safeguard against unauthorized access and potential security breaches.
Complete Controller Monitoring
The CPU Unit actively monitors events throughout the Controller, encompassing Units and EtherCAT slaves. Additionally, troubleshooting data is displayed in Sysmac Studio or on an NA-series PT. Furthermore, events are meticulously logged for comprehensive analysis.
Automation Software Sysmac Studio
Sysmac Studio provides an integrated development environment that seamlessly incorporates controllers, peripheral devices, and EtherCAT devices. Moreover, it offers a comprehensive platform for streamlined development and efficient management of automation systems.
It provides uniform procedures across all devices, supporting controller application phases, including design, debugging, simulations, commissioning, and real-time adjustments.
A Wealth of Simulation Features
The many simulation features include execution, debugging, and task execution time estimates on a virtual controller.
System Configurations
Introduction to the System Configurations of the NX-series Controllers
The NX Series supports the following system configurations.
Basic System Configurations
The NX-series provides two configurations: EtherCAT Network and Support Software.
In the EtherCAT Network, the built-in port connects to devices, ensuring precise control. Alternatively, the Support Software facilitates connectivity by linking to the CPU Unit’s USB or EtherNet/IP port. Furthermore, this seamless integration enhances flexibility in device communication.
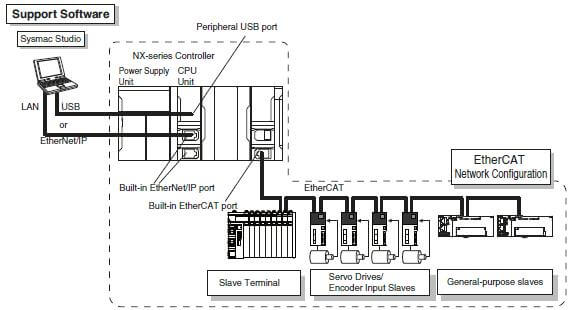
NX-series System Configuration Example
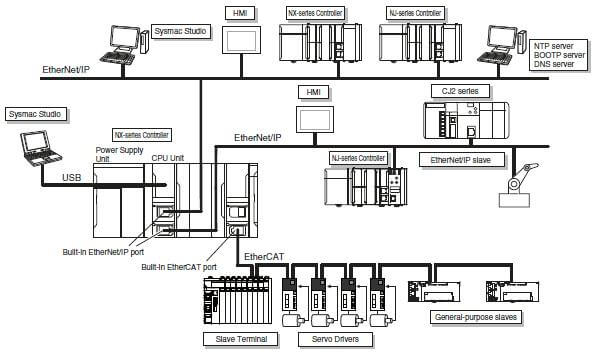
Introduction to the System Configurations of the NJ-series Controllers
The NJ Series supports the following system configurations.
Basic System Configurations
The NJ-series basic configurations include the EtherCAT network configuration, CJ-series Unit configuration, and the Support Software.
- EtherCAT Network Configuration enables seamless connection to a variety of EtherCAT Slave Terminals. Additionally, it supports analog/digital I/O slaves, Servo Drives, and encoder input slaves through the integrated EtherCAT port. This comprehensive configuration not only fosters connectivity but also ensures precise sequence and motion control, minimizing deviation for enhanced performance.
- In addition to the EtherCAT network, CJ-series Basic I/O Units and Special Units can be mounted on both the CPU Rack and Expansion Racks.
- The Support Software seamlessly connects to the CPU Unit’s peripheral USB port using a standard USB cable or alternatively, through an Ethernet cable linked to the built-in EtherNet/IP port. Additionally, it provides a flexible interface for users, allowing them to choose between a standard USB connection and an Ethernet connection for optimal convenience.
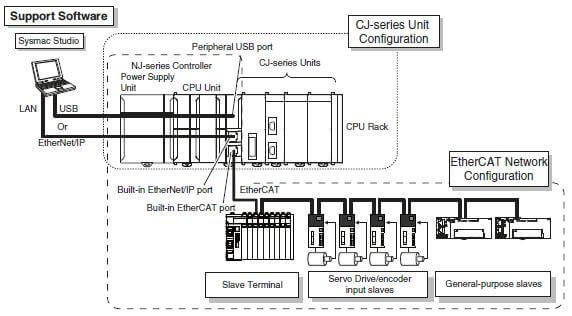
NJ-series System Configuration Example
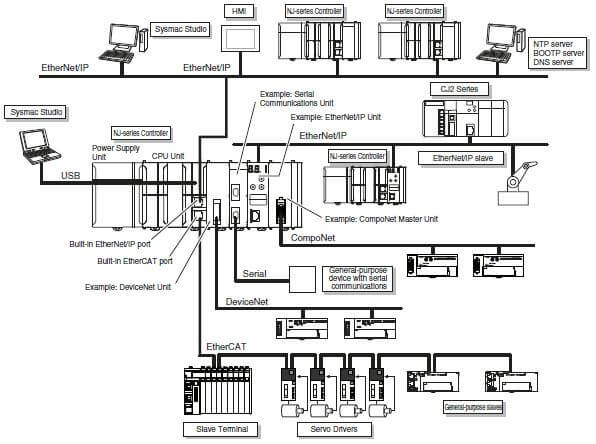
CPU Unit Operation
The NJ/NX-series CPU Unit seamlessly executes user program tasks, such as sequence and motion control, I/O refreshing, and external communications, utilizing its internal software. Additionally, it effectively manages these functions through the integration of advanced programming features.
It stores settings, user programs, and variables. Moreover, it utilizes these variables to access the CPU Unit, I/O, and external communications. This integration of internal software and variable usage, in turn, enables seamless sequence and motion control.
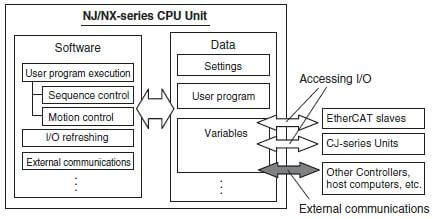
Program Organization Units (POUs)
A POU, as defined in the IEC 61131-3 user program execution model, constitutes a fundamental unit. Additionally, these units are combined systematically to form a complete user program.
There are three types of POUs, as described below
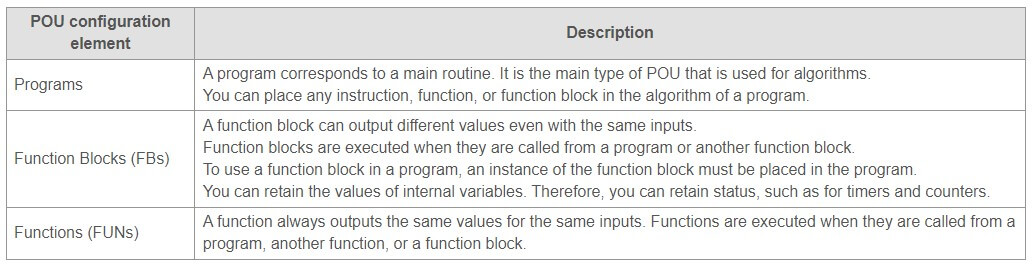
Easy-to-Read-Programming
To manage programs effectively, function blocks and functions divide processes into smaller units. Additionally, by utilizing function blocks, you can seamlessly reuse instances of these blocks in other devices requiring the same processes. This not only enhances efficiency but also promotes a modular and scalable approach to programming.
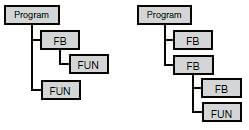
Reusable Programming
To manage programs effectively, function blocks and functions divide processes into smaller units. Additionally, by using function blocks, you can seamlessly reuse instances of these blocks in other devices requiring the same processes. This not only enhances efficiency but also promotes a modular approach to programming.
Accessing I/O with Variables
Within the CPU Unit, user programs use variables to access assigned I/O data. Moreover, the table illustrates the allocation of I/O and variables in the CPU Unit. The type of variable employed by a CJ-series Special Unit depends on the specific data it needs to access.
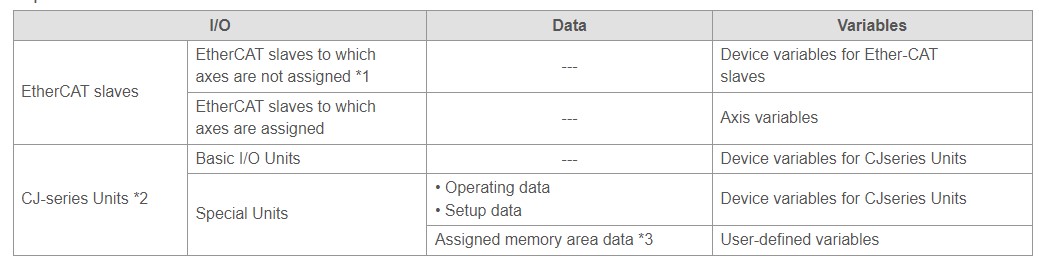
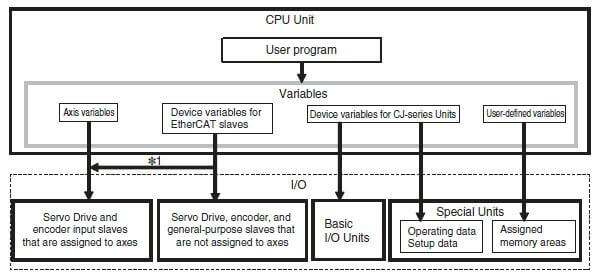
Introducing Omron NX5 Series Machine Automation Controller
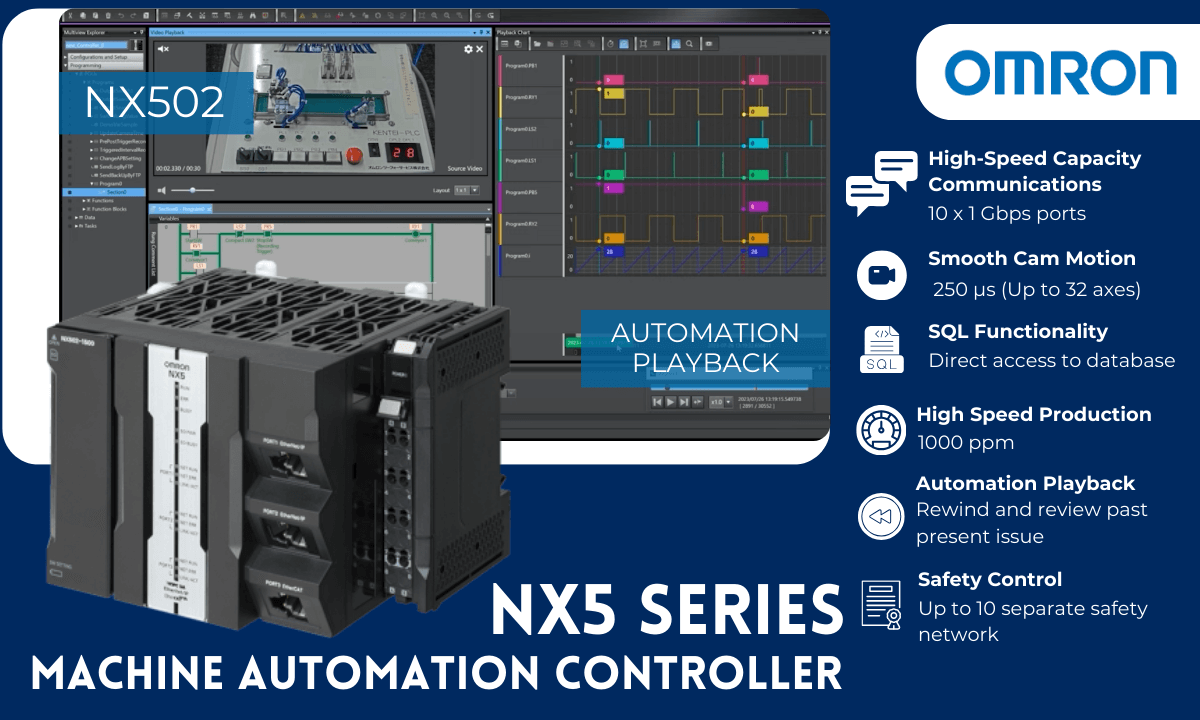
Leveraging Omron’s advanced information processing, communication technologies, and extensive memory, the new NX502 CPU and NX-EIP201 EtherNet/IP units enable real-time analysis and process modularization. This strategy enhances sustainability, reduces waste in production, and shortens lead times during line changes.
Interested to find out more about Omron Next Generation Machine Automation Controllers? Feel free to contact us!