Servomotors / Servo Drivers
What is a Servomotor and What is a Servo Drive?
A servomotor, part of a servo system, operates in tandem with a servo drive and comprises a motor driving the load and a position-detecting element, typically an encoder.
This system precisely adjusts parameters like position, speed, or torque to match the target value, ensuring precise machine operation.
Servo System Configuration Example
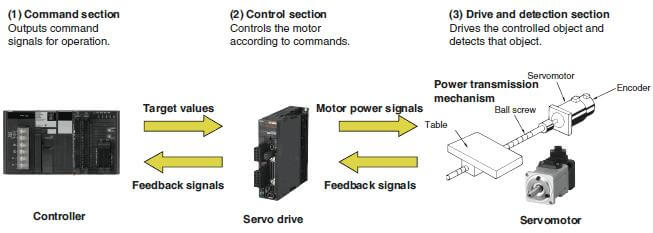
Features
Precise, High-speed Control
Servomotors excel in position and speed control, offering precision and flexibility.
They maintain performance at high speeds and correct deviations caused by external forces, thanks to encoders.
Fully-closed Loop
The most reliable closed-loop system is a fully-closed loop, employed when precision is vital. It directly reads the machine’s position via a linear encoder, eliminating the need to compensate for gear backlash, feed screw pitch errors, or torsion/expansion issues.
Fully-closed Loop System Configuration Example
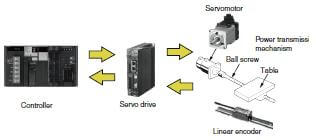
Semi-closed Loop
This method is commonly used in servo systems
Compared to an open-loop system, the Semi-closed loop offers greater speed and positioning precision. Typically, an encoder or similar detector is mounted behind the motor, measuring the rotation angle of a feed screw (ball screw) and providing feedback on the machine’s travel position. This indirect position detection differs from direct detection.
The characteristics depend on where the detector is installed
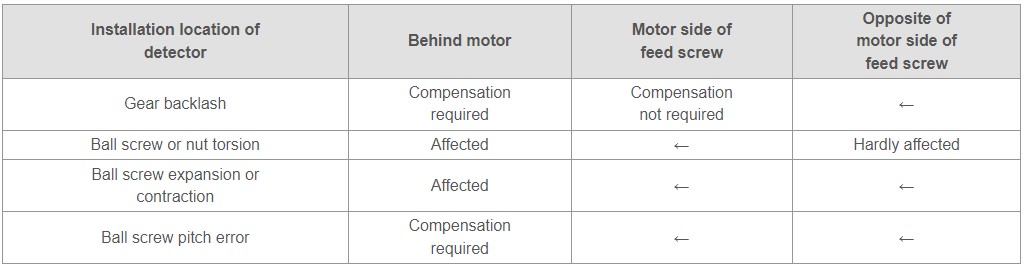
Semi-closed Loop System Configuration Example
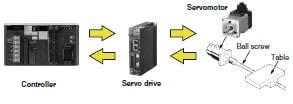
Open Loop
A stepper motor is used instead of a servomotor.
In open-loop control, simplicity and cost-effectiveness are key, but it can’t compensate for gear and ball screw issues or stepper motor stalls. It’s suited for low-precision, low-speed, and low-load-change applications.
Open Loop System Configuration Example
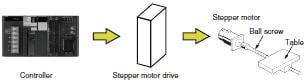
Principles
Servo Operation and Configuration
A closed-loop control system employs servo drives and servomotors, continuously comparing actual motor parameters with command values. The servo drive corrects motor operation in real-time based on error feedback, ensuring optimal system performance. This process is known as closed-loop control.
The control loop is managed by the servo drive, motion controller, or both, depending on the specific control needs. Position, speed, and torque control loops are employed independently as needed. Some applications necessitate only torque control, while others require current and speed control. Still, others need all three control loops for precise position control.
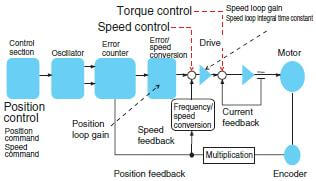
Servomotor
Industrial servomotors, primarily brushless, feature a powerful permanent magnet in the rotor. The stator contains multiple conductor coils that drive the rotor’s rotation when energized in a specific sequence. Rotor motion depends on stator parameters like frequency, phase, polarity, and current, provided in the correct timing.
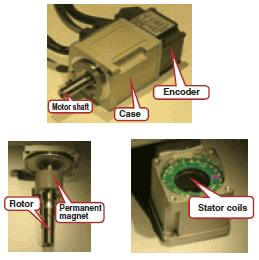
Encoder
Servomotors differ from regular motors due to their encoders, enabling precise and high-speed control based on provided position and speed commands.
Encoders, integral to servo systems, provide speed and position feedback. They’re often integrated with servomotors. In some instances, encoders are independent units placed apart from the servomotor, serving additional parameters beyond motor control.
Servo Drive
Servo drives execute host controller commands, regulating motor torque, speed, or position. Inputs from a motion controller, feedback encoder, and the motor itself guide control, with the servo drive delivering power as needed.
The fundamental operation mimics inverters, converting AC power to DC power, and then to a specific frequency to drive the motor.
In addition, a servo drive performs these functions:
- Establishes communication with the motion controller.
- Reads encoder feedback and makes real-time closed-loop control adjustments.
- Processes I/O tasks, including safety components, mode inputs, and operational status signal outputs.
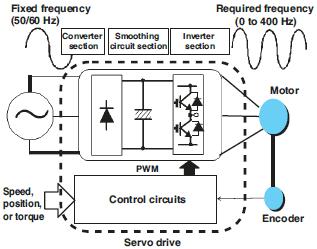
Interested to find out more about Omron Servomotor machine operations? Feel free to contact us!