Introduction
The key to energy performance is a reliable source of accurate data and analysis. Elaborate metering systems are often expensive to install, operate, and maintain. Data loggers are simple, robust measurement and recording devices that help companies save significant energy costs. The first step to reducing costs is identifying energy waste. Data provided by monthly utility bills and equipment ratings, while useful, are not sufficient.
Permanent metering is often not an attractive alternative because of high cost and uncertain returns. Simple, temporary devices, such as HOBO® data loggers, can be used to quickly obtain critical information at a fraction of the cost. A comprehensive metering system can be added later if analysis justifies a larger investment.
Information collected by data loggers can help validate the need for investment in improvements. Buying new energy-saving equipment requires capital, and operational changes can involve risk. Savings estimated through analysis of collected data helps justifies these projects.
In addition, with data loggers and a comprehensive understanding of utility charges, your facility will be more competitive with lower fixed costs. This white paper covers seven (7) common opportunities to find hidden energy waste, how to gather and analyze data, and how to calculate savings for each opportunity.
Monthly utility bills and equipment specifications do not provide enough information; actual measurements are essential to finding energy-saving opportunities.

Energy Waste #1: High Fixed Electricity Usage
Utility invoices report electricity usage over a billing period of about 30 days. This is important information, but it’s only part of the story. Average electric load for each demand interval (15, 30, or 60 minutes) is also helpful for understanding usage and uncovering opportunities. Example demand interval data is illustrated below.
This information is often available from your local utility company. Alternatively, you may use a simple load current data logger to obtain the information. When logging demand interval data, measure one phase and make these assumptions.
• Balanced 3-phase circuit
• Nominal line voltage
• Power factor of 90%
• Average real power [kW] = 1.732 x line voltage x average load current x power factor / 1000
These steps will help acquire demand interval data accurate enough for energy management:
1. Collect data for one complete utility billing cycle and compare actual real energy [kWh] from the utility invoice to the logged data. A small difference is expected because of the above simplifying assumptions.
2. Calculate a correction factor and use it on subsequent calculations. This will correct for actual line voltage, phase unbalance, actual power factor, and measurement errors.

These steps will help acquire demand interval data accurate enough for energy management:
- Collect data for one complete utility billing cycle and compare actual real energy [kWh] from the utility invoice to the logged data. A small difference is expected because of the above simplifying assumptions.
- Calculate a correction factor and use it on subsequent calculations. This will correct for actual line voltage, phase unbalance, actual power factor, and measurement errors.
These steps will help acquire demand interval data accurate enough for energy management:
- Collect data for one complete utility billing cycle and compare actual real energy [kWh] from the utility invoice to the logged data. A small difference is expected because of the above simplifying assumptions.
- Calculate a correction factor and use it on subsequent calculations. This will correct for actual line voltage, phase unbalance, actual power factor, and measurement errors.
Use demand interval data and portable loggers to investigate fixed loads and eliminate those not required to run all the time.
Fixed Usage
The interval data reveals that facility load has a strong daily profile. While peaking around 100 kW, the load rarely dips below 25 kW. This is called the “fixed load” – the amount of power that is used all the time, no matter the time of day or activity within the facility.
It is important to know the major components of fixed load – specifically, what pieces of equipment are causing this load? Using portable data loggers, a chart like the example below can be developed to understand fixed load and identify unnecessary loads that can be switched off instead of running all the time.

Energy Waste #2: Inefficient Air Compressor Control
Compressed air is a convenient way to deliver energy to industrial equipment and is also useful in many other ways. Unfortunately, it is also inefficient and wasteful. Less than 10% of the input energy ever does useful work, and 70% of the input energy is converted to heat at the compressor.
One important aspect of the compressed air system is compressor control. If you have more than one air compressor, it is very important to understand how the machines share the load. Air demand in the plant changes and rarely matches the rated output of all machines, so one or more machines must run at less than 100% output.
Partially loaded compressors are not as efficient as fully loaded machines.

The best way to share the load is to base-load all except one machine, which is designated as the “swing machine.” The swing machine maintains system pressure by changing the output of the compressor as needed. All other machines are operated with constant output at their maximum efficiency point, or are idle if not needed to meet the load.

Data loggers are used to verify proper machine loading as follows:
- Install a data logger and current transducer on one phase of each compressor and record load current for one week using a sample interval of 30 seconds.
- Calculate compressor input power at each interval assuming nominal voltage and 86% power factor using the expression Input Power [kW] = 1.732 x nominal line voltage x line current x 0.86 / 1000
- Graph input power for all machines on one graph and verify that only one machine at a time operates at partial load.
Other important observations – study your compressor input power profiles and consider:
- What does it cost you to operate your air compressors for a year?
- Does compressed air usage follow production activity?
- How much energy (and money) is wasted on compressed air when the facility is idle?
- How much of the compressor output do you think is leakage in the distribution piping?
- What is the value of the waste heat, and how could it be used?
Energy Waste #3: Off Centerline Operation
Formal energy management systems have energy performance indicators (EnPIs) that are used to manage energy performance “by exception.” They tell leadership how actual energy performance compares to expectations. At the highest level, a monthly EnPI may be “total electric and gas energy used [MWh].” No additional action is needed when the EnPI is as expected (on centerline).
Total energy is often adjusted for actual weather conditions and production level to avoid wasting time investigating variance that’s easily explained by weather conditions or changes in production that month.
When the top EnPI is off centerline, something is not right. Leadership will want an explanation and action plan to return the facility to peak energy performance. This is when portable data loggers are used on individual equipment such as large motors, compressors, or process equipment to investigate and determine the cause of the problem. In addition to process equipment, the investigation should include:
- Air compressors and vacuum pumps
- Air handlers, make-up air units, and other HVAC equipment
- Large fans and pumps
This is also a time to record and closely analyze demand interval data for the main electric supply.
Many users do not know when the peak usage occurred, or which electric loads contributed to the peak. Average electric load [kW], recorded every 15 minutes, is very useful in reducing peak power (demand) charges.

Energy Waste #4: Temporary Fixes
Data loggers are often used to make significant reductions in energy usage and cost. Unfortunately, these gains are not always sustained over time. Within six months to a year, energy usage returns to higher levels. The cause of this problem is often “temporary” changes that are forgotten and become permanent. You must manage temporary changes to sustain your savings over time.
Example
A high-speed machine that places labels on soup cans is malfunctioning. In order to meet production targets, it’s essential to get the machine working properly as soon as possible. The operator thinks increasing compressed air pressure will help, so pressure is increased (in the entire plant) by 5 psi. The problem persists, so other alternations are made to lighting, the HVAC system, etc. and the machine eventually begins to work properly.
In a typical plant, that is the end of the story; problem “solved.” In reality, the short-term problem may be solved, but those temporary alterations are now permanent with unintended consequences, like increased operating cost.
To be fair, the floor mechanics did their job, which is to get the machine running; that should not change. However,
- Did anyone really understand the problem and its causes?
- Were alternative solutions considered?
- Was the best long-term solution implemented? To all the above questions, the answer is “probably not.”
Recommendations
- Encourage your floor mechanics to continue supporting production and implementing short-term fixes.
- Require those same mechanics to report all temporary modifications so a formal problem-solving methodology that leads to the best long-term solution can be implemented.
- Don’t let a series of unreported, temporary modifications permanently increase your energy costs.
Follow up on temporary changes and implement the best permanent fix to sustain your energy performance gains

Energy Waste #5: Excessive Peak Energy Use
Imagine driving an automobile from New York to Seattle without a working speedometer. Three weeks after arriving in Seattle, you receive several speeding tickets and a $1,000 fine for exceeding the limit in Iowa, South Dakota, and Wyoming. The value of real-time speed indication is obvious; you may have been able to avoid the violations, or at least would be aware of when and where they occurred. The same is true of commercial and industrial electric loads.
Most commercial and industrial electric rates include energy charges [¢/kWh] and peak power (demand) charges [$/kW]. Many users do not know when the peak usage occurred, or which electric loads contributed to the peak. Average electric load [kW], recorded every 15 minutes, is very useful in reducing peak power (demand) charges.
Data loggers are used to obtain load profiles as follows:
- Install a data logger and current transducer on one phase of the electric mains for the facility and set the sampling interval to 1 minute. If the service exceeds 600 amps (maximum size CT available) and there are multiple conductors per phase, place the transducer around one of the conductors and assume current is identical in all conductors.
- Calculate average power over a 15-minute interval assuming nominal voltage and 90% power factor using the expression (Power [kW] = 1.732 x nominal line voltage x line current x 0.90 / 1000). A spreadsheet program is helpful.
- Study the profile and look for significant peaks in energy usage
as in this example:
A small grocery store had a peak load of 359 kW at 8:00 every morning caused by simultaneous defrosting of all freezers (red line). The green line shows the resulting load profile one week later, after the timers where offset to avoid the peak load. Billing demand was reduced from 359 kW to 302 kW, resulting in annual savings of almost $10,000.

Know when your peak usage occurred and which electric loads contributed to the peak. Average electric load [kW], recorded every 15 minutes, is very useful in reducing peak power (demand) charges.
Interested to know how we can help you save energy cost? Feel free to contact us!
MORE INTERESTING ARTICLES
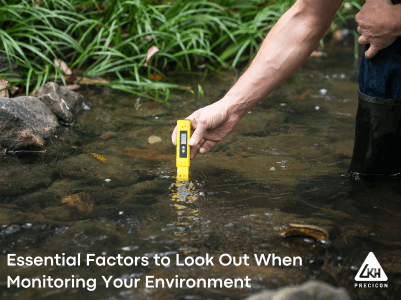