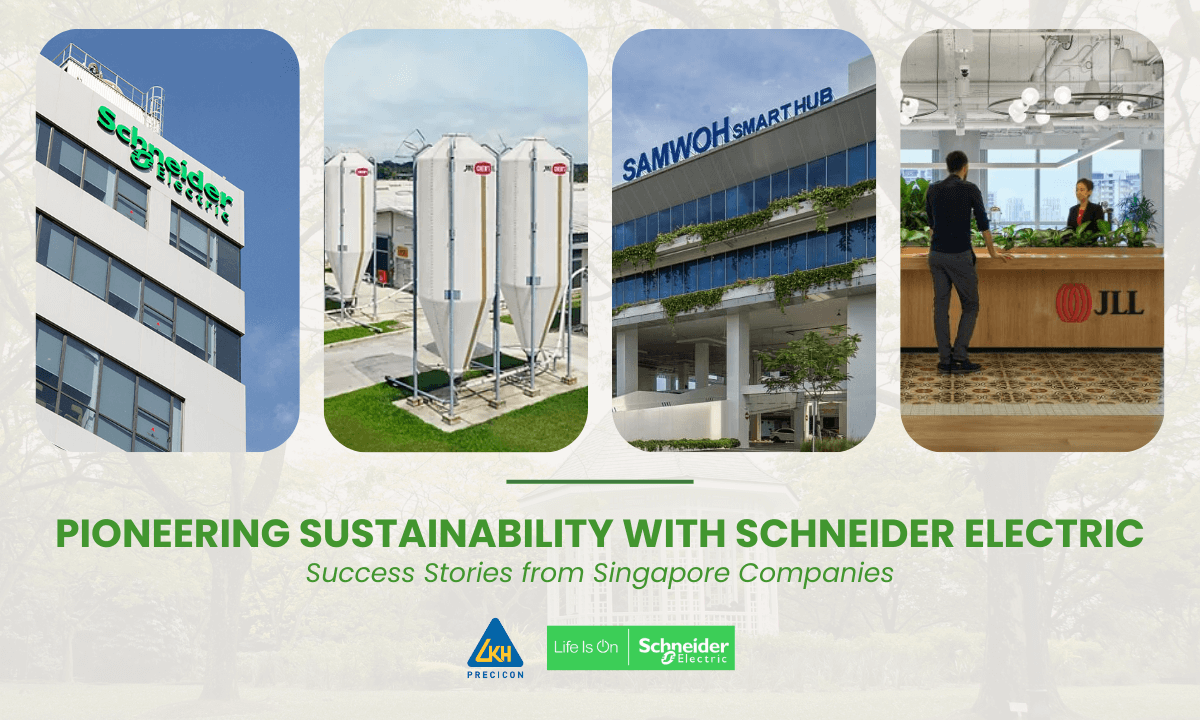
In recent years, the push for sustainability has gained significant momentum across the globe, and Schneider Electric, alongside various Singaporean companies, has been pioneering this movement. This article compiles an array of success stories that highlight the innovative sustainability solutions implemented by Schneider Electric and leading companies in Singapore.
Smart and Connected Retrofit Building
Schneider Electric’s East Asia and Japan headquarters at Kallang Pulse exemplifies a property that has been greened to meet sustainability standards. In 2018, Schneider Electric retrofitted the 25-year-old multi-tenant building with their EcoStruxure solutions, incorporating green connected products and renewable energy to reduce energy usage by 45%. Centralising activities in one location and utilising energy-efficient architecture made this possible.
Today, Schneider Electric’s East Asia Headquarters at Kallang is the first large-scale Innovation Hub in Singapore, hosting over 4000 visitors annually from over 20 countries. Additionally, the green building is the first brownfield, mixed development building to receive the prestigious Green Mark Platinum Zero Energy Award by the Building and Construction Authority Singapore, substantiating the effectiveness of Schneider Electric’s EcoStruxure solutions and other green connected products, such as the PowerTag and Environmental Sensors.
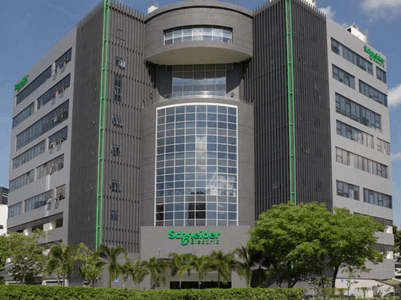
Some of the results include:
- Saved about 122,000 kWh of electricity and 3,700m3 of water per year from 2018 to 2020.
- With Passive and Active Energy Reduction and EcoStruxure Microgrid Advisor, electricity consumption is reduced by up to 45%.
- The Building runs on 100% Green Energy (onsite and offsite) renewable energy (with solar blended power supply) full day beginning from April 2021 with delegated iRECs.
- Carbon emissions reduced by 1,650 tonnes p.a., which is equivalent to 353 cars (2.0cc) off the road.
Moving towards making an IMPACT on sustainabilty efforts, Schneider Electric partnered with several other local orgranisations to transform their operations.
Chew’s Agriculture – Securing Singapore’s Food Future
Chew’s Agriculture is one of three egg farms in Singapore, with over 35 years of history. At their previous location, they faced frequent breakdowns due to the age of their equipment and facilities. As operations were automated houses, an inconsistent power supply would disrupt ventilation, feed, and waste management, thus affecting the chickens’ well-being. Subsequently, causing a domino effect on eggs production and the overall business. Then came the challenge when Chew’s were relocating their farm and were seeking a reputable partner to digitalise operations.
Chew’s needed a digital solution to:
- Ensure stable supply
- Improve operational resilience, reliability, and business efficiency
- Future-proof operations for sustainable growth
Chew’s engaged Schneider Electric for the development of their new facility. Schneider Electric installed the EcoStruxure Asset Advisor, PowerTag, and other green connected products at Chew’s new site in Kranji.
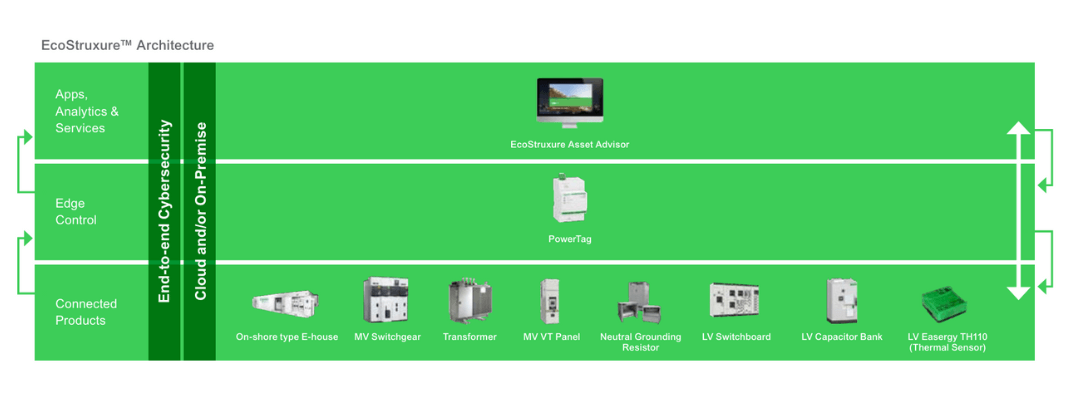
Schneider Electric’s EcoStruxure Solution helped maintain ventilation, egg collection, lighting and feeding system at an optimum level. The platform allowed Chew’s to collect data from a connected product in the main switch room such as thermal sensors. All these information and data is put together in a single dashboard, which is readily accessed and helps reduce maintenance downtime by 10%. In a nutshell, engaging Schneider Electric allowed Chew’s to become more resilient, adaptable and capable of ensuring Food Security for Singapore in a sustainable way.
Samwoh Smart Hub – Paving the Way for a Greener Future
Samwoh is transforming Singapore’s construction industry by developing innovative technologies and sustainable solutions. The Samwoh Smart Hub and Innovation Center is a testament of Samwoh’s commitment to R&D, contributing to a future with greener built environment. In 2021, Singapore set three targets, known as ‘80-80-80 in 2030,’ to achieve a low-carbon, greener built environment by 2030. Construction companies like Samwoh Corporation play a crucial role in driving this transformation. Therefore, to equip their Smart Hub with energy-efficient and smart features, Samwoh partnered with Schneider Electric and a local system integrator.
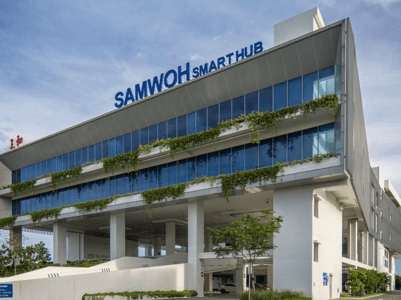
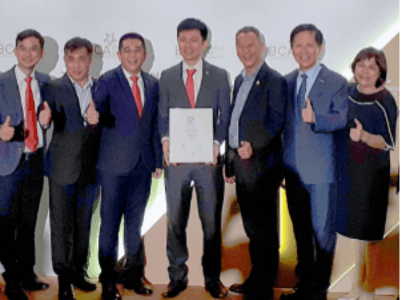
Schneider Electric helped the company to achieve the prestigious BCA Green Mark Platinum Positive Energy for Industrial Buildings Award. Schneider’s EcoStruxure solution helped them gain complete visibility and control of the building’s energy utilisation. The connected products are integrated into a single ecosystem, and seamlessly collects real-time data on energy consumption and production. Smart sensors implemented throughout the building optimises temperature and humidity and increase efficiency up to 50%. From the positive energy generated by the solar panels to electricity utilised throughout the building, Samwoh Corporation has the means to monitor, analyse and optimise their energy usage to make informed decisions.
Together with Schneider Electric, Samwoh Corporation continues to lead Singapore’s construction industry for sustainability.
JLL APAC Headquarters – The Optimal Workplace Experience
Global property services leader JLL adopted a smart approach to infrastructure management to support business recovery. JLL aimed to consolidate four offices across Singapore into a state-of-the-art space that offered an exceptional human experience. They needed an engaging, people-centric work environment for the new generation that was also hyper-efficient and sustainable. Schneider Electric’s Light and Room Control EcoXpert Partner played a crucial role in designing and delivering this solution.
The comprehensive building solution features over 150 IoT-enabled sensors for monitoring space utilisation, people movement, and air quality. Wireless PowerTag energy meters are used for energy monitoring throughout the system. SE 8000 Room Controllers manage lighting, blinds, and kinetic sculptures, while integrated audio-visual systems ensure convenient control.
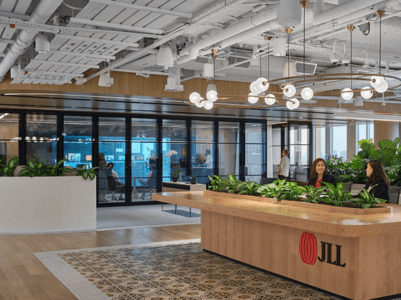
Building management tasks are automated by the EcoStruxure Building Operation application and networked automation servers. The application includes an Energy Expert module that tracks energy use, meet conservation objectives, and detect, diagnose and respond quickly to any power-related issues. The EcoStruxure Building Advisor connects JLL to a team of experts that proactively monitor and maintain building performance.
Such solutions has resulted in a JLL being a Grade A office, setting a new benchmark for workplace environment. The new smart office significantly reduces operating costs, boosts productivity, and enhances staff satisfaction. It carefully manages thermal comfort and well-being, offering employees greater engagement and a seamless user experience.